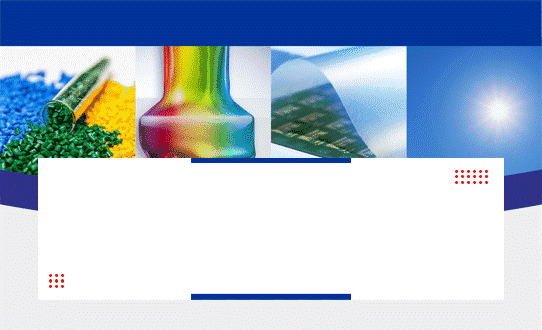
Laboratory coating equipment serves as a cornerstone in research and quality assurance for various industries, including automotive, aerospace, medical devices, and electronics. By providing precise and reproducible coatings, these instruments ensure that critical performance parameters such as adhesion, corrosion resistance, and surface finish meet stringent industry standards.
To ensure the accuracy and reliability of coating test results, it is necessary to prepare standard coatings that meet specific requirements. According to product standards, uniform coatings with a specified thickness must be prepared on designated substrates, forming the basis for coating tests.
Various countries have established standard methods for coating preparation, such as ASTM D823, outlines several practices for producing films of uniform thickness on test panels, addressing factors such as substrate preparation and drying conditions, and ASTM D3022, focuses on determining the consistency and drying properties of specific coatings. The Chinese national standard GB/T 1727-1992 provides comprehensive guidance on substrate treatment, coating application, and environmental conditions, forming a solid foundation for coating performance evaluations. In daily production control, commonly used tools for preparing samples include different types of applicator, which can produce wet film coatings ranging from a few microns to over a thousand microns in thickness.
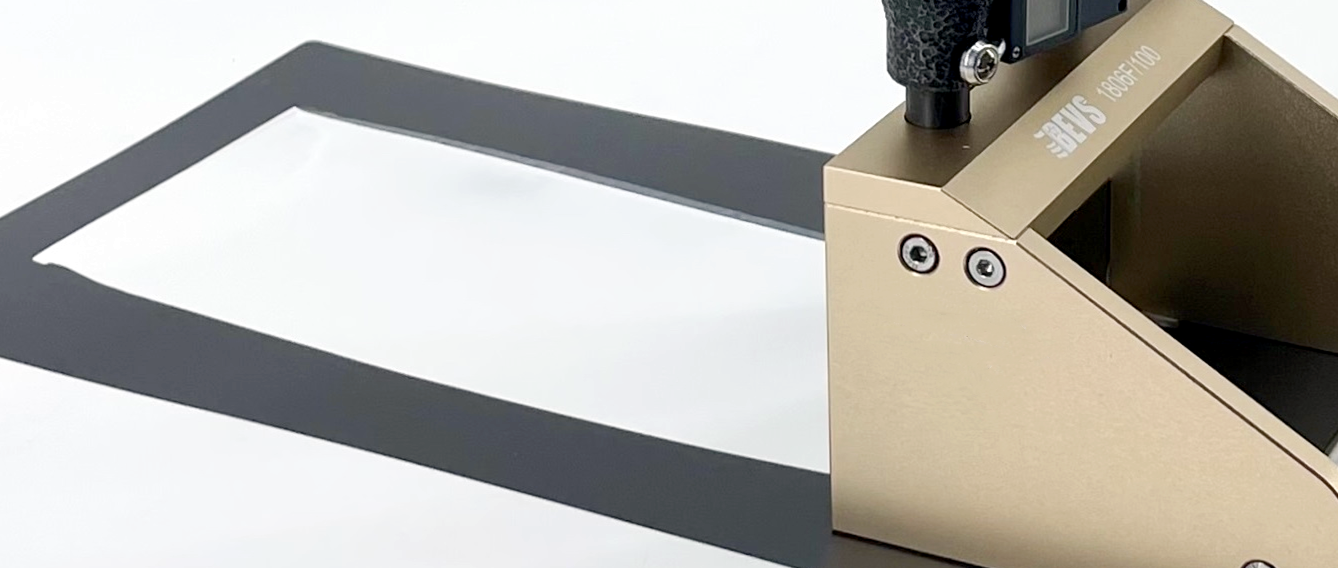
Coating Equipment and Tools
BEVS, a manufacturer of paint and coating testing instruments, offers precise coating equipment and tools. The typical applicators available on the market can be categorized into two types based on their operation mode: automatic film applicators and manual applicators.
The Automatic Film Applicator is a laboratory instrument designed to evenly apply liquid coatings, inks, adhesives, and other substances onto test substrates. This process creates uniform and traceable films for repeated testing of coating thickness, color, quality, and other performance parameters. It is widely used in industries such as paints, inks, plastics, cosmetics, and medical devices for coating applications and quality control.
Automatic film applicators incorporate advanced features such as programmable speeds, adjustable applicator gaps, and precision substrate holders. For instance, in the automotive coatings industry, these tools are indispensable for testing the durability and UV resistance of clear coats under controlled laboratory conditions.
When using a laboratory film applicator, process parameters such as the speed of the applicator, the gap between the applicator and the substrate, and the amount of material to be coated must be carefully controlled. During the coating process, factors such as uneven substrate surfaces, inappropriate applicator settings, and material viscosity variations can result in defects like pinholes or irregular film thickness. Besides, due to the varying properties of different samples, specific requirements during the laboratory coating process—such as maintaining a constant temperature, heating, or vacuum adsorption—may differ. Improper use or settings can lead to uneven coatings, which may affect the quality and performance of the final product. Employing advanced equipment with features like vacuum-assisted substrate holders or heated application environments can mitigate these issues and ensure consistent film quality. In addition, different types of film applicators are available to meet varying needs.
Modern film applicators simulate manual operation, applying more uniform force and maintaining a consistent speed to minimize or eliminate errors caused by manual factors such as coating speed, direction, and pressure. The applicator itself does not control the film thickness; this is usually managed using high-precision applicators or wire bars to achieve greater coating accuracy. Selecting the appropriate applicator depends on the type of material to be coated, the type of substrate, and the desired film thickness.
BEVS bar coater adopts cold extrusion processing technology to process concave and convex wavy curves on the surface of the steel rod, so as to achieve better coating. It can reach the min. thickness of 4μm.
The Single Sided Applicator is particularly suited for applications in paints and adhesives where minimal material usage and high reproducibility are required, such as in testing scratch resistance or flexibility.
The applicator is made of high grade stainless steel and is easy to clean, both models can be used with automatic film applicator. Model 1808 has two different inlet slopes which makes the test samples range wider and the test results are more ideal.
Four Sided Applicator With Reservoir
The item is made of high grade stainless steel with reservoir, four gaps in one makes it meet various film application demands.
The Four Sided Applicator is versatile for multi-layer film applications in research environments, allowing users to evaluate different coating formulations simultaneously.
The applicator is made of high grade stainless steel and is easy to clean. Four gaps in one applicator makes it more suitable for the lab.
Digital Ajustable Applicator
The Adjustable Digital Applicator is designed according to ASTM D823E. It consists of two precise digital micrometers, a high precise scraper and a special alumina frame.
The Adjustable Digital Applicator offers unparalleled precision for achieving exact film thickness, making it ideal for applications in microelectronics where thin-film uniformity is critical for device performance.
To sum up, laboratory coating equipment plays a vital role in ensuring the precision and reliability of coating applications across various industries. The choice of appropriate applicators and meticulous control of process parameters are critical to achieving desired coating performance. As coating technologies continue to evolve, advanced tools such as automatic film applicators and digital adjustable applicators offer enhanced precision, efficiency, and adaptability to meet diverse testing and production needs. These innovations not only streamline laboratory processes but also contribute to higher standards of quality and consistency in the coatings industry.